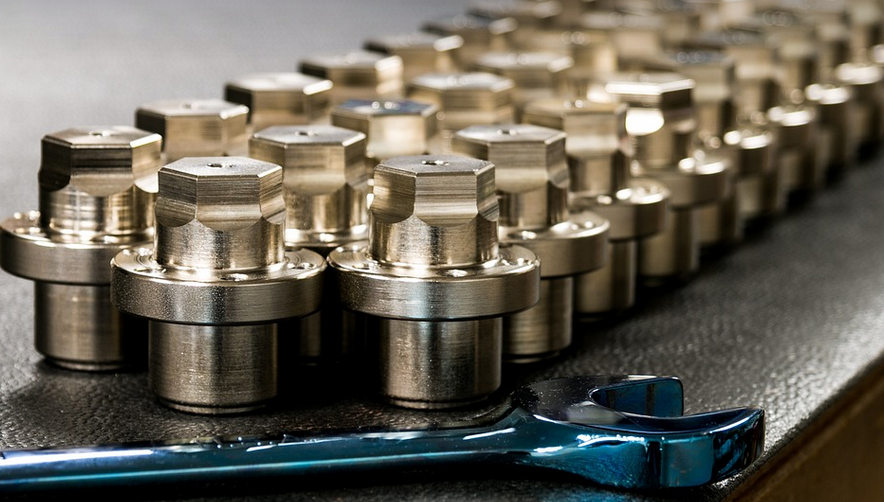
Laser Cutter Filtration System: Ensuring Clean Air & Optimal Performance
The Importance of Proper Filtration in Your Laser Cutting Operation
Let’s face it, laser cutting is a precision craft that demands meticulous attention to detail. From the initial setup to the final cut, every step in the process requires a keen eye and an understanding of the intricate nuances involved. One crucial aspect often overlooked is the importance of proper air filtration – a topic we’ll delve into with a focus on its direct impact on your laser cutting operation.
Laser cutters, while incredibly precise, generate considerable dust particles during their operation. These microscopic particles, in conjunction with other airborne contaminants such as metal shavings and toner particles, can pose significant challenges to the integrity of your work environment. Neglecting proper filtration puts your equipment, materials, and even your health at risk.
Unraveling the Benefits of a Comprehensive Filtration System
A robust laser cutter filtration system goes beyond mere dust mitigation; it offers a comprehensive approach towards enhancing productivity and ensuring optimal performance across various facets:
– **Safety First:** The primary benefit lies in the enhanced safety of your workforce. Reduced exposure to airborne particles mitigates the risk of respiratory problems, eye irritation, and allergies, promoting a healthier work environment.
– **Extended Equipment Lifespan:** The constant flow of dust and debris can significantly wear down your laser cutter’s components. A high-quality filtration system minimizes this wear and tear, ensuring long-term performance and extending the lifespan of your equipment.
– **Improved Material Quality:** Laser cutting involves intricate material manipulation, often with delicate, precise cuts. Dust particles can interfere with the accuracy of your cut lines. Effective filtration ensures a clean working environment, ultimately leading to superior-quality final products.
Understanding the Components of a Powerful Filtration System
A powerful laser cutter filtration system encompasses multiple vital components that work synergistically to ensure optimal performance:
– **Air Intake:** This is the foundation of your filtration system, responsible for drawing in ambient air. High-quality intake systems with pre-filters effectively capture large debris and dust particles, preventing them from entering the machine.
– **Filter Media:** The heart of any filtration system lies in its filter media. These specially designed materials, ranging from HEPA filters to electrostatic precipitators, utilize various technologies to trap microscopic particles. The choice of filter media is crucial and depends on your specific application needs.
– **Ducts and Piping:** The intricate network of ducts and piping ensures the even distribution of filtered air throughout your workspace. These ensure efficient airflow and minimize any potential backflow or obstruction within the system.
Choosing the Right Filtration System: A Guide for Your Needs
Selecting the right laser cutter filtration system can feel overwhelming, but with a clear understanding of your needs, you can make an informed decision:
– **Dust Level:** The level of dust and debris generated during your specific cutting process dictates the required filtration level. Higher-volume cutting necessitates more robust systems for optimal efficiency.
– **Material Type:** Certain materials, like wood or certain metals, create different levels of particulate matter. Some filters are specifically designed to handle various types of particles, ensuring efficient processing of diverse materials.
– **Budget and Space:** Consider your budget constraints and the available space within your workspace when choosing a filtration system. Some systems offer compact solutions that maximize efficiency while others require larger installations for optimal performance.
Putting it All Together: Ensuring Optimal Performance
A comprehensive laser cutter filtration system is not just about installing equipment; it’s about building an ecosystem that promotes clean air, high-quality cuts, and long-term equipment durability.
To truly maximize its potential, ensure you have:
- Regular maintenance checks: Keep your filtration system in top condition by regularly cleaning filters, inspecting ducts, and following manufacturer guidelines.
- Proper training for operators: Teach your team about the importance of this crucial aspect and how to operate the system efficiently.
- A well-ventilated workspace: Ensure adequate ventilation throughout the work area to prevent build-up of dust and particles.
By investing in the right filtration system, you’re not just protecting your equipment; you’re investing in the overall success of your operation.