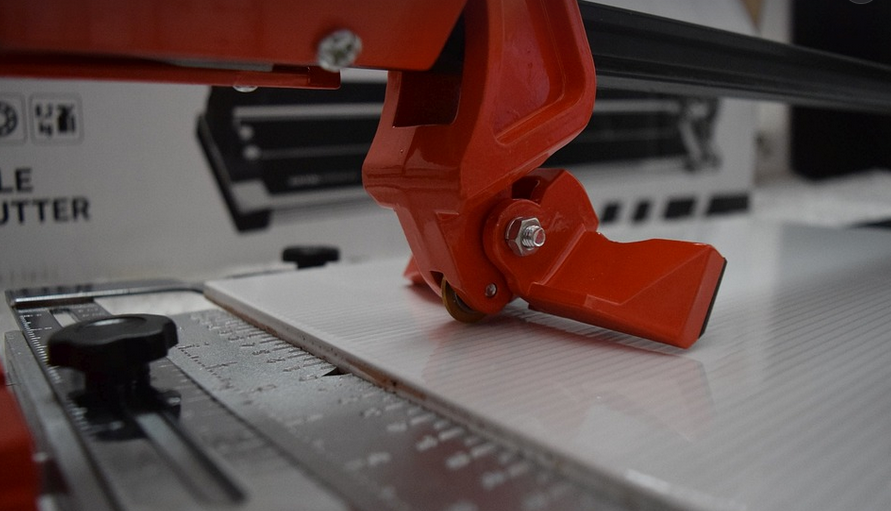
Diaphragm Pump Air Consumption: Understanding The Flow Of Your System
What are Diaphragm Pumps and how do they work?
Diaphragm pumps are a type of positive displacement pump that uses a flexible diaphragm to create suction and deliver fluids. Unlike many other types of pumps, their operation is based on the mechanical action of this diaphragm, which creates pressure in the pump chamber. This pressure then drives liquid through the system, and it can handle a wide range of applications.
These pumps are often used for transferring liquids in various industries like food processing, pharmaceuticals, agriculture, and water treatment. Their versatility stems from their ability to handle viscous fluids, chemicals, and even abrasive substances. The diaphragm’s flexibility enables them to adapt to changes in fluid viscosity and pressure, making them a robust choice.
Why is Air Consumption Important?
The air consumption of a diaphragm pump is an essential factor when considering its efficiency and overall performance. Understanding this concept provides valuable insight into the pump’s power usage and potential challenges. In simpler terms, it is the amount of air that a pump needs to draw in or use to move the fluid.
The need for air consumption in diaphragm pumps arises from their operation. These pumps rely on a precise balance between suction pressure created by the diaphragm or piston moving against a pressure chamber and the volume of air needed to create this suction. Excessive air consumption can lead to inefficiency, reduced performance, potential damage to the pump, or even safety hazards.
Factors Affecting Air Consumption
Several factors influence a diaphragm pump’s air consumption:
- Pump Design and Size:** The size of the diaphragm pump directly influences air consumption. Larger pumps typically consume more air, due to the increased volume of fluid being moved.
- Fluid Type and Viscosity:** The viscosity and density of the fluids being pumped play a crucial role in air consumption. More viscous fluids require more air to be drawn in for suction, as their consistency demands a greater effort from the pump to move them.
Measuring Air Consumption
Measuring the air consumption of a diaphragm pump can be done using dedicated tools and techniques:
- Air Leakage Measurement:** This involves observing for leaks in the system, which directly impacts air consumption. If there are leaks, it’s crucial to fix them as they add unnecessary air usage.
- Pressure Gauges and Calibrations: These gauges measure the pressure differential within the pump chamber. By measuring this difference between the suction and discharge pressures, we can get a clear picture of how much air is being used for creating suction.
Minimizing Air Consumption
Here are some techniques to minimize air consumption in diaphragm pumps:
- Optimizing Pump Configuration: This can be achieved by adjusting the size, shape, or material of the diaphragm and chamber. A well-designed pump will have a smaller air leakage rate.
- Choosing the Right Air Intake: The quality and location of the intake directly impact air consumption. Optimize this by ensuring the intake is properly sized and positioned for efficient suction.
Impact on Pump Performance
Minimizing air consumption leads to better pump performance, ultimately leading to several benefits:
- Increased Efficiency: This directly translates to greater energy efficiency and lower operating costs for the pump.
- Reduced Wear and Tear: Pump operation is smoother with reduced air consumption, contributing to a longer lifespan for the diaphragm and other components.
Conclusion
Understanding air consumption in diaphragm pumps is essential for maintaining efficiency. By carefully considering factors like pump design, fluid properties, and optimization techniques, you can minimize air consumption and enhance your system’s performance to achieve optimal results.
Let me know if you have any other questions! I’m happy to provide more information or help you understand this concept further.